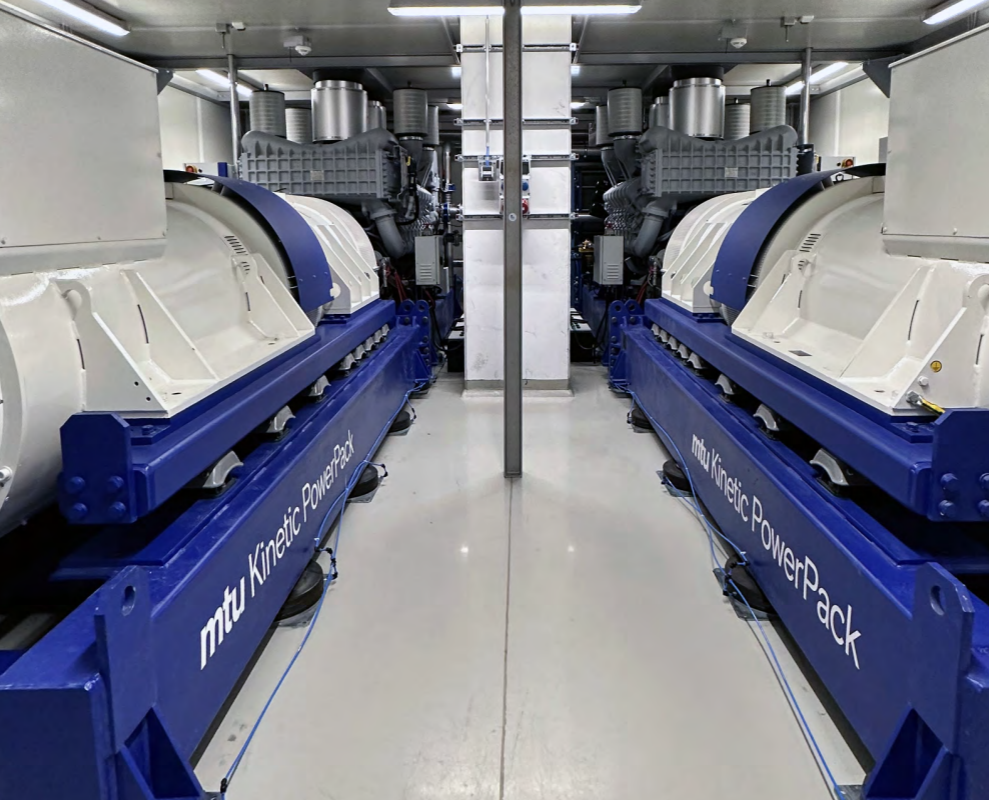
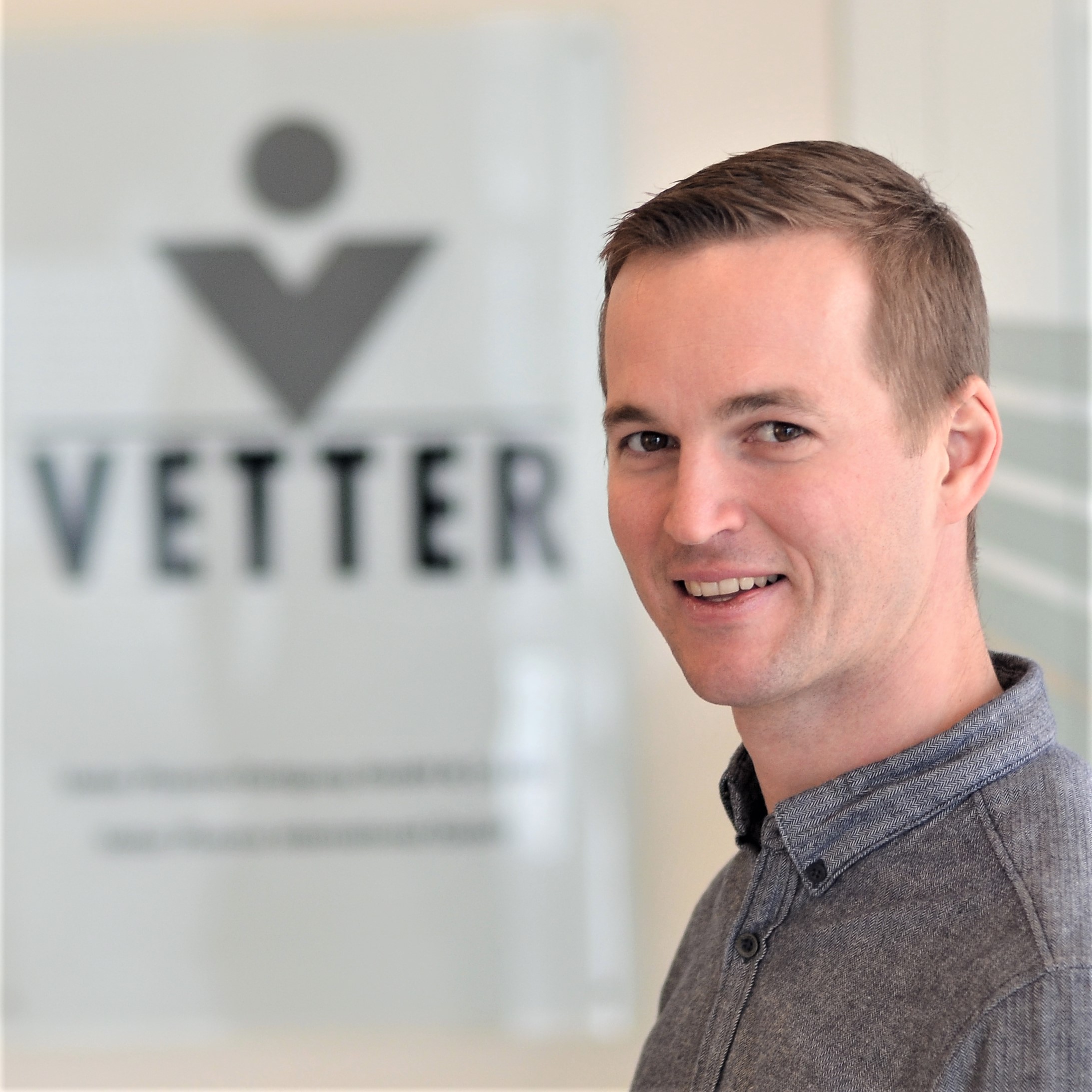
Kai Schumacher, Head of Electrical Engineering at Vetter, explains the importance of power supply and provides insight into how Vetter, as a fill finish CDMO, addresses this issue.
What can cause power interruptions?
Power interruptions, failures and fluctuations can have various causes. Power fluctuations specifically refer to the variation in voltage and power levels which occur in an electrical system. They can be triggered by influences on the grid side including voltage peaks, network failures and short interruptions, also known as micro-cuts. Accidental disruptions to power cables, like those caused by thunderstorms or construction in the area, may also be a cause. These fluctuations, along with voltage spikes (overpower) and undervoltage (underpower) can negatively affect the consistent flow of power.
How can even minor voltage fluctuations cause a disruption in pharmaceutical production?
When a power deviation occurs, equipment can easily malfunction, resulting in reduced efficiency or even complete shutdown. Maintaining a reliable power supply is critical to the smooth operation of pharmaceutical facilities. Voltage and frequency must be stabilized to prevent damage, that can ultimately be costly and harmful to customer’s products. If fluctuation occur, the systems react to changes in the pre-set limits, potentially result in long-term delays and reduced productivity that are difficult to recover from.
Aseptic manufacturing is particularly vulnerable because equipment operates within a narrow voltage range. Any fluctuation or loss of power can cause production systems like ventilators, cooling generators and production machines to stop, potentially leading to the loss of cleanroom status and compromising the safety and efficacy of pharmaceutical products.
In the worst case, this can lead to the loss of an entire batch, which has an impact on the customer's supply chain. The consequences of power interruptions can extend far beyond the cleanroom environment, affecting the health and well-being of patients who rely on these medications.
What kind of equipment is used to face the challenges of power supply?
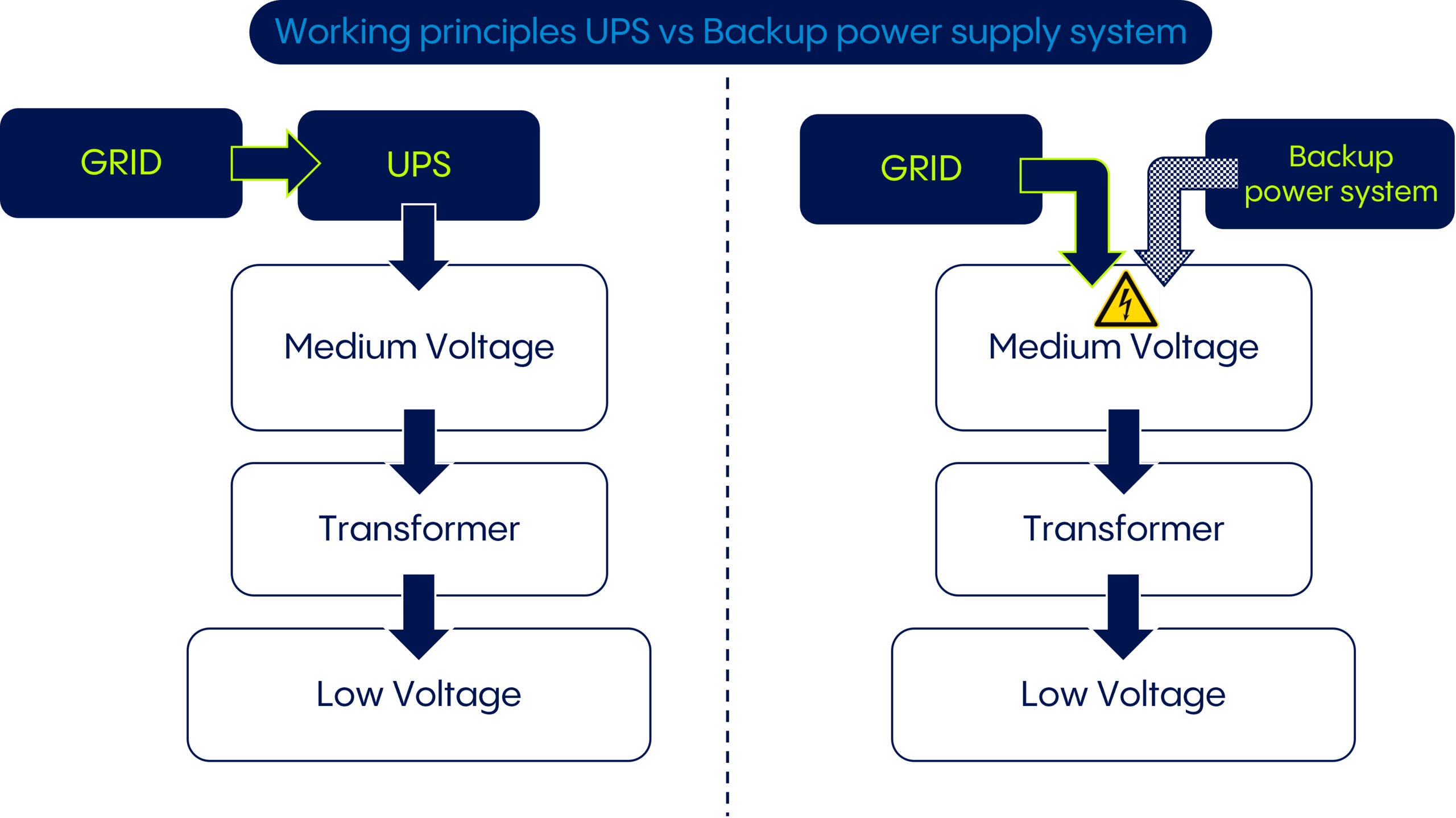
There are various technologies and equipment types available to secure power supply, including ancillary equipment such as smart grid sensors and energy storage systems such as batteries. However, two primary technologies can be used to address the risk of power interruption: emergency generators and uninterruptible power supply systems (UPS).
Back-up power generators are more commonly known. Most hospitals, for example, use them to deal with loss of power. These typically diesel engine-driven generators convert mechanical energy to electrical energy and are not connected to the grid. In the event of a power failure, the unit kicks in and takes over the power supply of the plant.
However, it requires a short window of time for the equipment to reach full operating level, so while it is a reasonable solution to prevent power outages, it does not function as an uninterruptible power supply.
UPS systems, on the other hand, are always on standby and connected to the upstream grid. They come in two formats: static and dynamic. Static UPS systems usually use batteries as a backup power source. When the power supply is normal, the batteries are charged through the power grid. If the power supply is interrupted, the UPS system switches to battery power to provide continuous power to all connected equipment. Static UPS systems are most often used in smaller applications and to provide short-term coverage due to the limitations of the batteries.
Dynamic UPS systems typically use a diesel generator in combination with a flywheel. When the power supply is normal, the flywheel is charged and stores kinetic energy. However, in the event of an interruption, the stored energy is released to power the connected equipment. Dynamic UPS systems are typically used in larger applications and critical facilities but can also be used for longer-term coverage because the engine can be powered by diesel.
Both static and dynamic UPS systems provide continuous and reliable power to critical equipment in the event of a power outage or other electrical disturbance. They disconnect from the grid and take over the power supply independently until the grid's energy flow is back to normal, preventing any harmful interruption to the power supply, no matter how short. The systems activate with no delay, preventing any harmful interruption, no matter how short, to the power supply.
Do most pharmaceutical companies already have countermeasures implemented?
The pharmaceutical and biotech industries players often have a backup power system in place to mitigate risks associated with power interruptions and fluctuations. However, the specific system used varies based on a company’s unique needs and personal experiences. Cost, manpower, and physical space are the primary constraints when implementing a power backup source, presenting challenges that are difficult to address once a system has been purchased.
In our experience, the investment in UPS systems pays for itself tenfold when reliability and quality are prioritized. To effectively mitigate power interruption risks, companies must plan for the size, capacity and cost of UPS systems when designing future production facilities, rather than trying to implement them after the fact.
Companies should familiarize themselves with available market solutions to find the most suitable option for their business, as it has its own requirements that may differ from another company, even in the same industry.
How does Vetter address the ‘power-supply-issue’?
Vetter was an early adopter of backup power systems. More than 20 years ago, we implemented our first dynamic UPS systems to protect our aseptic production sites. For other non-critical pharmaceutical sites, such as warehouses, Vetter uses backup generators.
Today, Vetter has 11 dynamic UPS systems at three commercial production sites with seven 1400 kW systems and four 1600 kW systems. Each site has multiple active UPS systems operating simultaneously. We incorporate UPS systems into each building layout prior to site construction and have a dedicated technical department with an electrical engineering team that is responsible for and trained to maintain the UPS systems. Both, investment costs and operating costs are planned at an early stage.
Power interruptions are usually beyond a company’s control. Vetter, for example, experienced 60 power fluctuations and interruptions at its production sites in 2023 alone. But in every case, the UPS systems activated and prevented any harmful disturbance.
It is critical for us to equip pharmaceutical production facilities with backup power systems and contingency plans to minimize the risks associated with potential power interruptions and provide a secure supply chain of drug products for our customers and their patients.