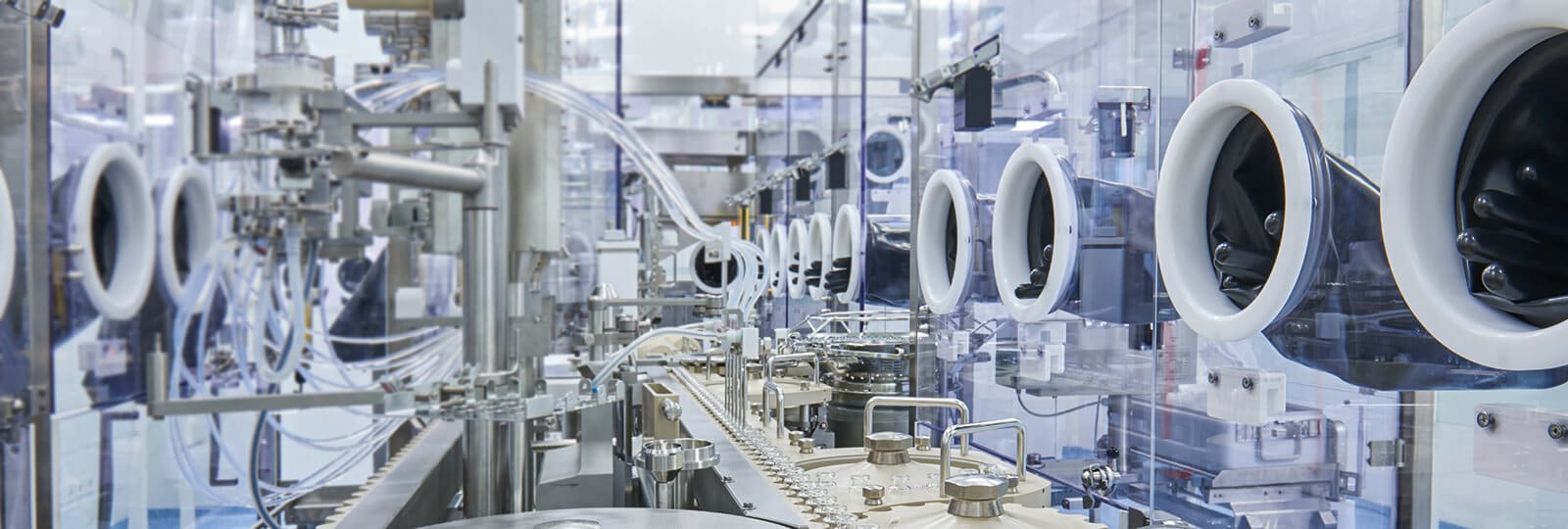
The requirements for aseptic filling are based on the specifications of authorities such as the FDA (Federal Drug Administration) or the EMA (European Medicines Agency), as well as to meet the needs of our customers.
As such, the further development of aseptic processes and technologies is a prerequisite for CDMOs (Contract Development and Manufacturing Organizations) if they want to meet either the requirements in terms of quality and flexibility or even set new standards.
Examples:
- The demand for specialized treatments (including orphan drugs) and prefilled delivery systems is increasing and changes the product portfolios of drug manufacturers.
- More flexibility is needed in order to meet format, packaging and filling requirements.
- Quality requirements on the part of authorities and customers are constantly increasing as with, for example, the expansions of Annex 1.
Aseptic filling
Aseptic filling processes take place in a sterile an environment as much as possible. Thus, machine parts are only used after having been sterilized, autoclaved or decontaminated.
In addition, the associated technologies are designed in such a way that any contact between an active ingredient and the environment is minimized which, for the most part, reduces the possibility of contamination.
Today, two different cleanroom technologies are used for this purpose: isolators and restricted access barrier systems (RABS). Both technologies have their advantages and disadvantages.
Isolator technology
Isolators are units that are completely isolated from the outside environment and are often considered the best solution for a high degree of sterility. Since isolators require extensive decontamination actions when changing products, they are best suited for manufacturing individual products in large quantities.
RABS technology
A barrier and a dynamic air flow ensure separation between the drug and its environment. RABS offers the advantage of faster set-up, more efficient product change and greater flexibility for the processing of different products. They also enable better use of filling capacity.
Further development of RABS
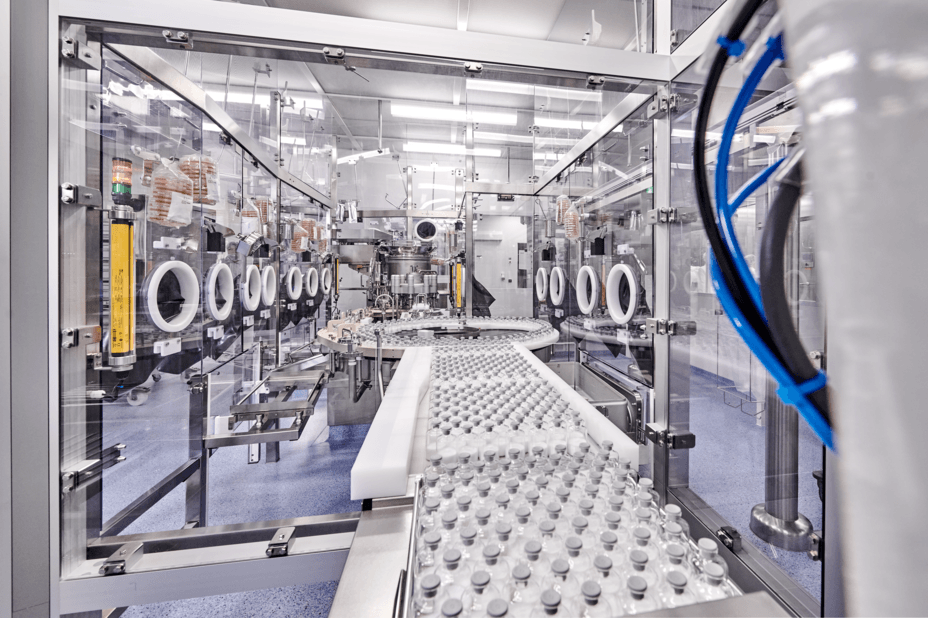
If manufacturers want to score points in terms of quality and flexibility, they have to ask how they can take advantage of both concepts. Vetter has answered this question with the development of an integrated cleanroom concept: V-CRT® (Vetter Cleanroom Technology).
V-CRT® makes it possible to achieve safety and quality standards that equal or even surpass the performance of isolators while still offering the flexibility advantages of RABS.
This innovative concept is based on the central idea of fully automated decontamination of the entire cleanroom, including RABS, using hydrogen peroxide (H2O2). V-CRT® is a two-barrier system that minimizes the risk of contamination and offers a number of advantages over existing concepts:
Rapid decontamination enables efficient product changeover
H2O2 decontamination of the entire cleanroom prior to each batch minimizes the risk of microbial contamination
Continuous online monitoring of multiple variables helps ensure the effectiveness of the decontamination process
The containment approach follows the concept of the closed system since the RABS doors are no longer opened following H2O2 decontamination.
After innovation is before innovation
The introduction of V-CRT® was an important milestone in the technological development of aseptic production at Vetter. However, innovation is not an end in itself and is why we are continuously developing V-CRT®.
A port system which is integrated in the second installation step, the so-called “liquid path,” will make it possible in the future to dispense with transfers of materials from grade B to grade A. In addition, in the future an H2O2 decontamination airlock between the grade-B and C areas will allow contamination-free transfer of non-autoclavable materials into the cleanroom.
Vetter’s goal is to offer reliable aseptic production with high quality. This purpose of this effort is to provide support for our customers in meeting the requirements of the changing biopharmaceutical market.
Vetter has been relying on RABS technology for decades. With the development of V-CRT®, we have succeeded in catching up with the isolator in terms of quality while at the same time, maintaining the usual flexibility. V-CRT® is currently available in three cleanrooms at Vetter. The intent is to implement the innovative technology in all cleanrooms.
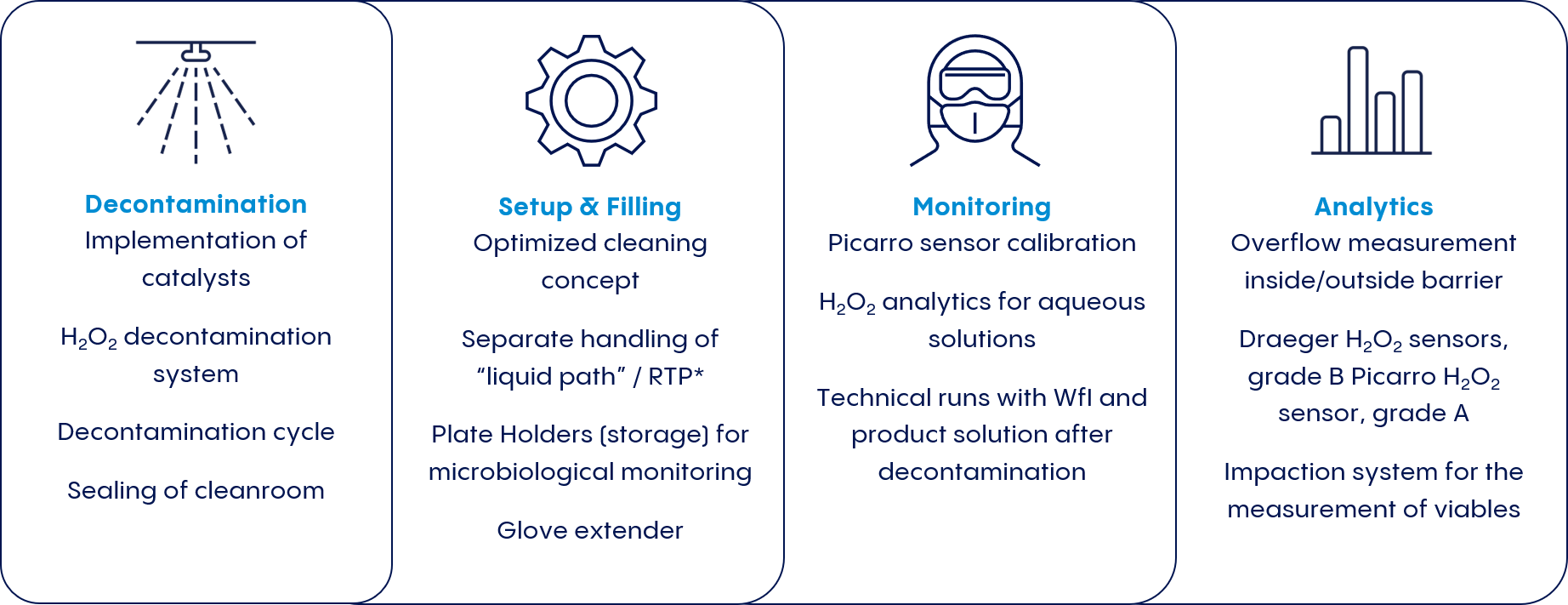