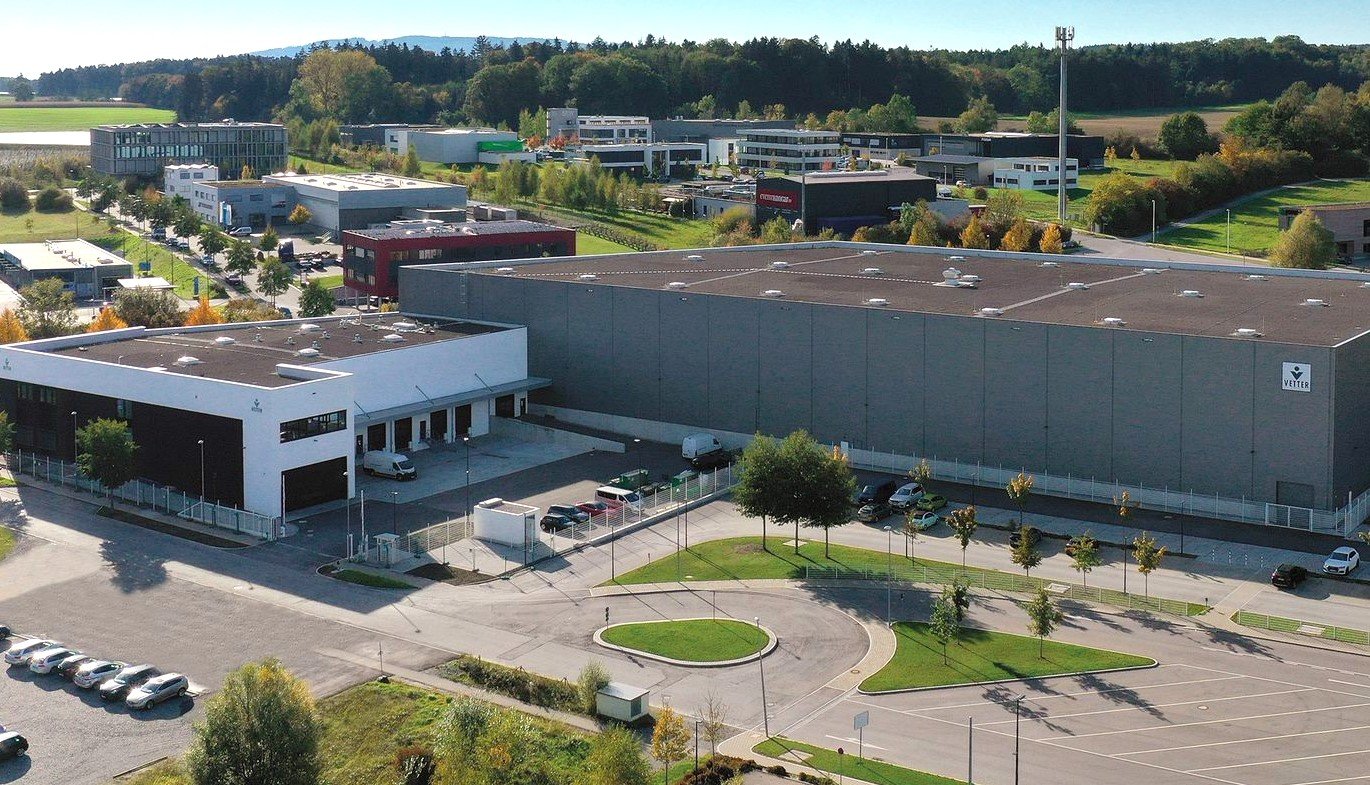
With a total investment of approx. 20 million euros, the new fully automated building provides storage space for materials with high-stock turnover rates such as packaging components and thus optimizing our logistical infrastructure. In addition, valuable capacity will be freed up in the existing warehouse.
Construction of the warehouse began in April 2021 and was designed to further address our strategic expansion plans. “We have already taken a process-related expansion concept into account during our planning process. The warehouse operation will initially start with a two-shift operation which can be extended to three shifts per day,” explains Peter Mayer, Senior Vice President Customer Project Management, Procurement and Logistics. The new storage facility includes 7,700 sq. meters of logistics space consisting of 1,200 sq. meters for incoming and outgoing goods and 6,500 sq. meters of room temperature storage with the capacity for more than 16,000 pallets and a shelf height of 14 meters. The state-of-the-art high-bay warehouse is equipped with automated forklifts and six positions for trucks on a receiving area ramp connected to the transfer area. Four driverless shuttles connect the transfer area with the building’s shelves while four driverless forklifts operate between them.
“The additional warehouse is a further testament of our commitment to support our customer’s supply chain needs,” states Managing Director Peter Soelkner. “We have also planned for more investment projects that will help us to continue the momentum of sustainable growth of our company.” The numerous investments at all our sites include the recently completed extension of the development service laboratories as well as a new multipurpose building at the Ravensburg South production site that houses laboratories for quality control, thawing rooms, offices and a new attractive employee canteen. The completion of another production building for aseptic manufacturing, at the CDMO’s Schuetzenstrasse site, is planned for the end of 2026, with several new cleanrooms to be realized in the subsequent years.
In addition, the implementation of further automated visual inspection machines is planned. Managing Director Thomas Otto summarizes: “Despite the multi-faceted challenges we currently face, such as pandemic as well as political and economic circumstances, we will continue to invest over the next years to expand our capacities in the areas of development services, aseptic filling, visual inspection and packaging to meet the increasing market demand. The planned expansions will go hand in hand with the optimization of the infrastructure across all our sites.”