The 2024 apprenticeship project
In their first year of apprenticeship, machine and plant operator apprentices at Vetter get to develop their own product and take on responsibility in the role of their own choosing. Their eyes light up with pride and enthusiasm when they talk about “the project.”
So, does Vetter make lighters now too?
"This year, absolutely," instructor Dennis Lieb says with a grin. "Last year it was a juicer." During the first of their two-year apprenticeship to become machine and plant operators, students learn the basics of metalworking. It starts with a two-month introductory course, followed by ten months of work on the annual project. The apprentices themselves choose the project they want to work on and help create the overall plan. The trainers’ job is to ensure that the project, curriculum, and available machines are all aligned. Then, in the second year of their apprenticeship, the students spend time working in pharmaceutical production.
This is how the lighters were made. Watch to the end to see!
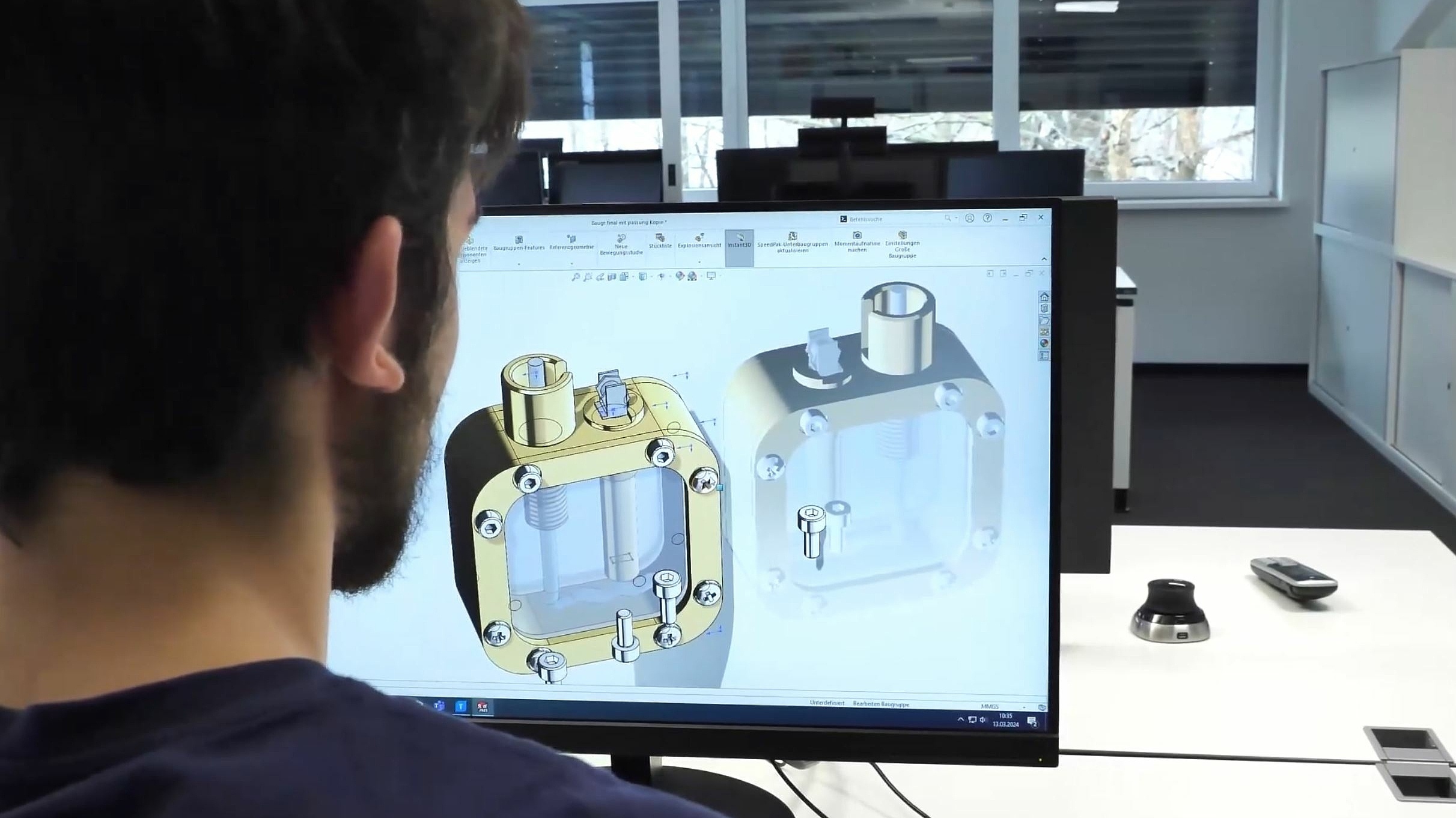
Insights from the project: The first spark
What do you want to do today? What do you need? What do you need to know?
Each morning begins with a stand-up meeting. The trainers ask the group: "What's on the agenda? Who’s doing what?" They give feedback on preliminary sketches and 3D printing prototypes and answer queries about turning, milling, drilling and filing. Allowing rookies to run the project gives them the chance to learn how to best use their skills to contribute to the team.
Frustration and satisfaction: the Aha! effect of learning
"Tolerating frustration is part of the process," says trainer Martin Meisterhans. "Sometimes you need to develop new approaches and discard ideas that you once thought were good. But it's the trainees who decide that, not we. This flexible approach to training is great for building relationships. You learn to lay your cards out and stand up for your ideas. And most importantly, you learn – perhaps for the first time – what you do want to achieve in your professional life and what you don't."
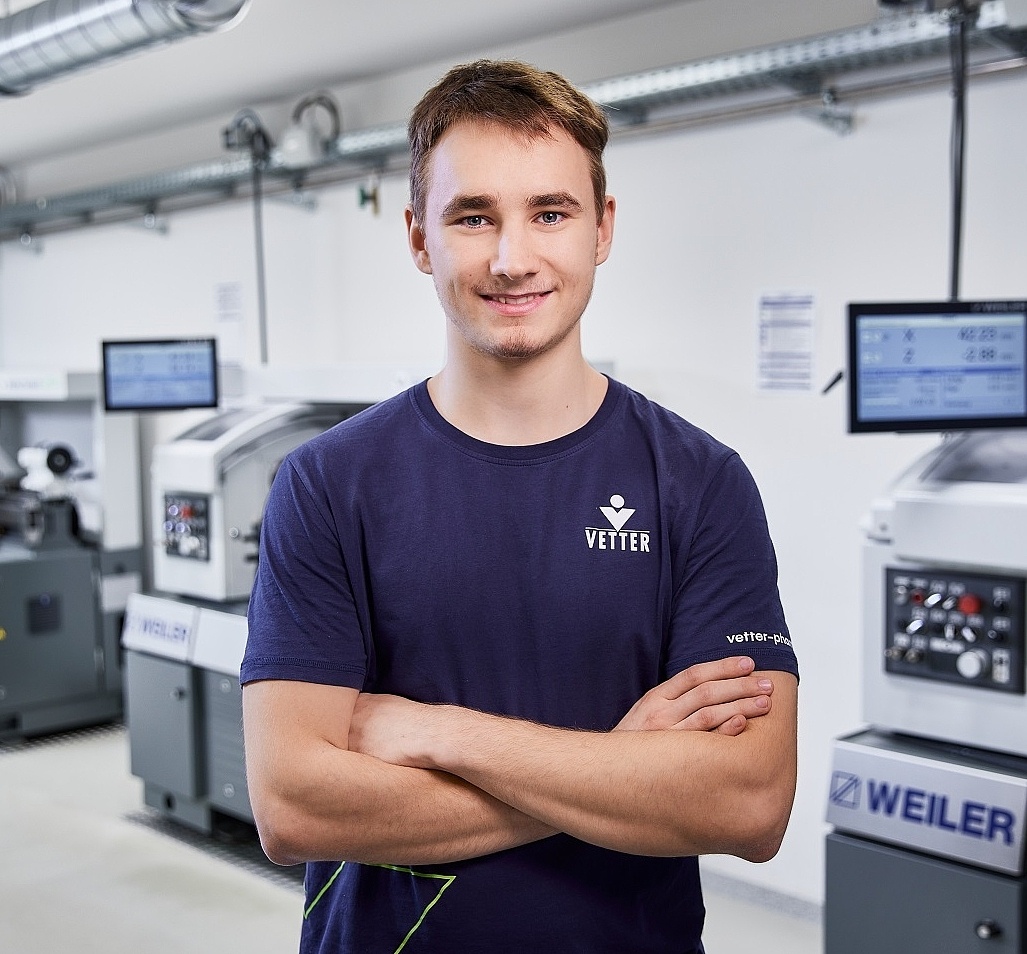
Samuel Kraus, apprentice
"Each apprentice had a different role in the project. At first, I was busy organizing the project, gathering all the apprentices’ ideas and putting them to a vote. As the project went on, I was thinking about how to solve problems that came up, like whether the acrylic glass will be watertight, and about how to manufacture the parts so that they’re as easy as possible to assemble and will still seal. In the end, it was a fantastic project, where the whole group put in a lot of effort and enjoyed themselves. And it's just fun to see everybody give their all day after day to make this a successful and special project."
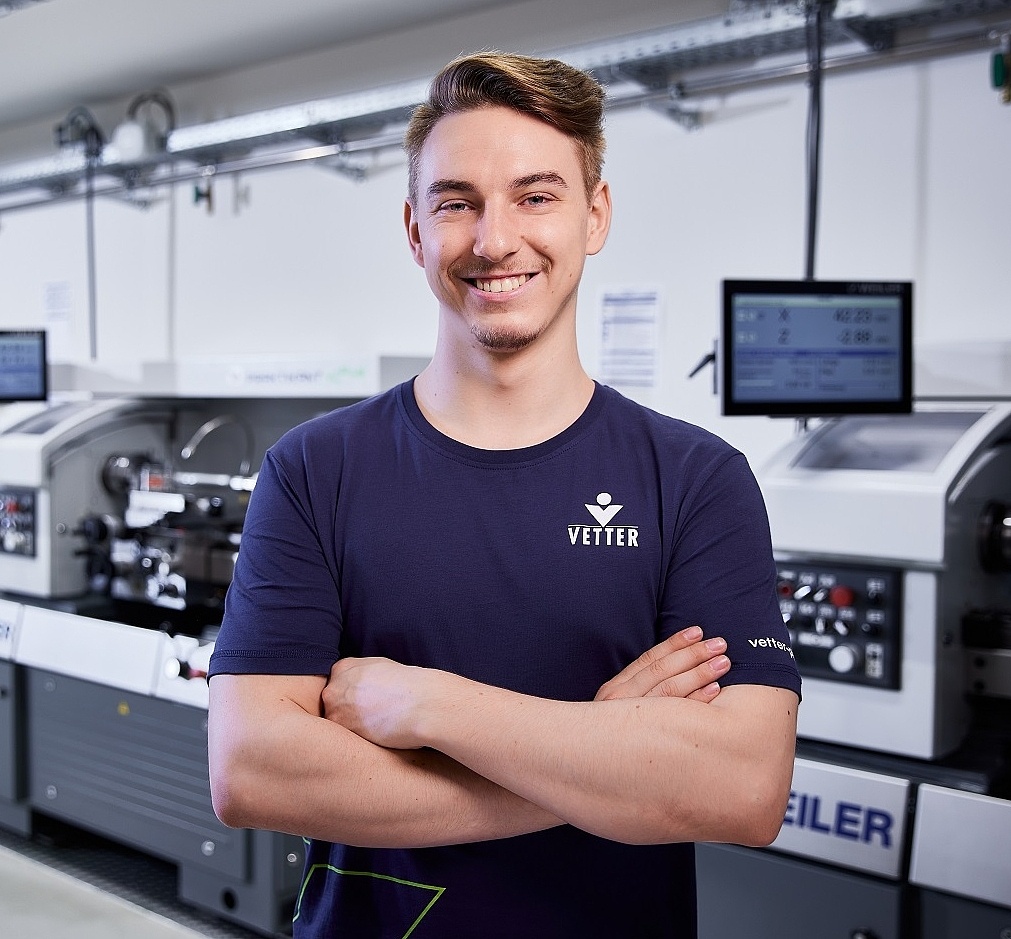
Florian Reichle, apprentice
"For me personally, the best part was at the end, when all the parts were done, and everything was laid out in front of you; assembling the lighter and seeing the pieces fit together and that the lighter worked. You could see how one after the other people assembling their lighters and wanting to try them out right away – and the relief and joy that followed when they lit up and stayed sealed. Everyone knew that their work, and everyone else’s, had led to a result that everyone was happy with and that profited everyone."
Agile training
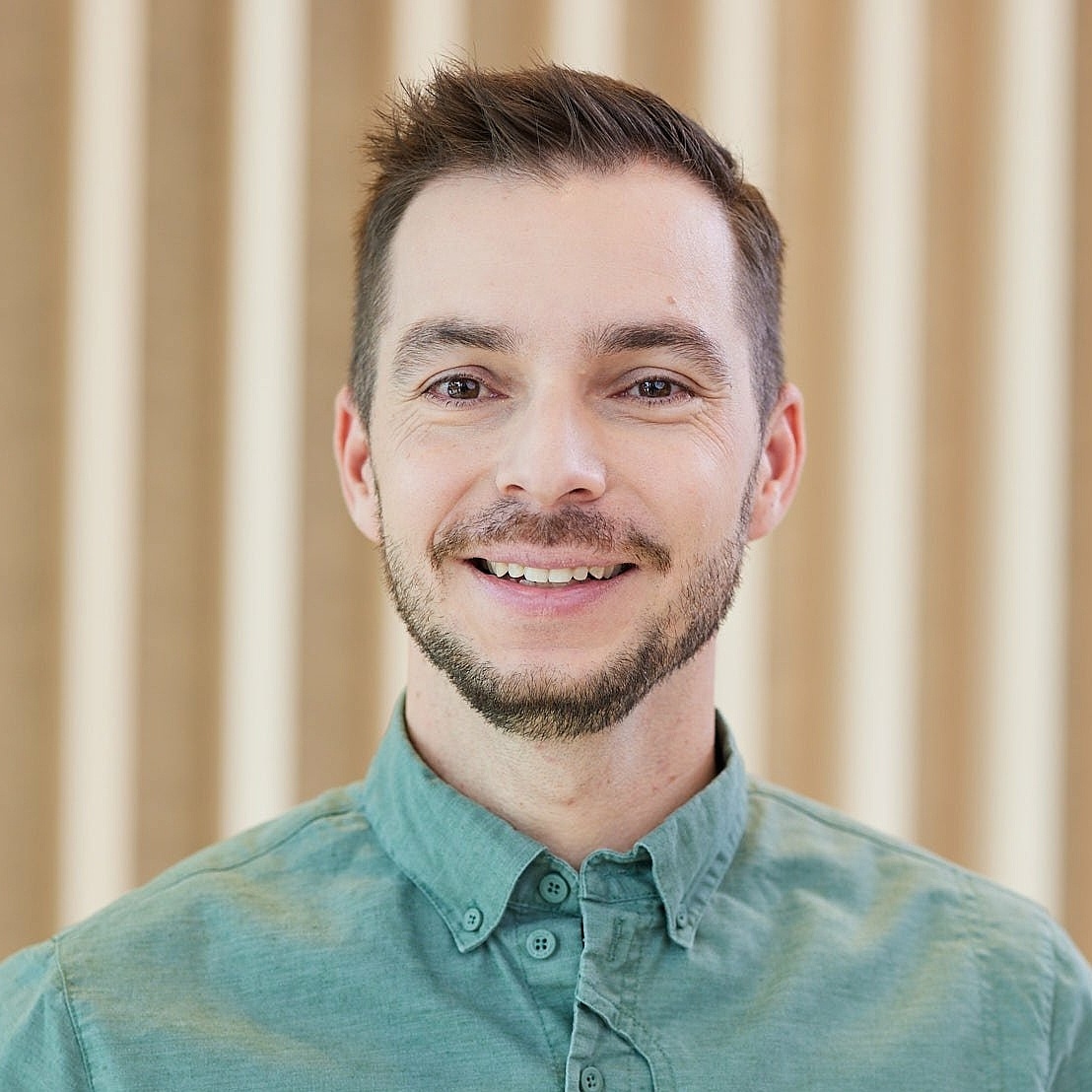
Agile training means going beyond the textbook and identifying and leveraging people’s unique strengths to help them be more motivated and to participate more.
Dennis Lieb, Manager Technical Training
Dennis Lieb knew pretty quickly that he wanted to become a teacher. In 2011, shortly after completing his own apprenticeship, he started teaching himself. "I was able to draw on both the negative and positive experiences of my own apprenticeship," he recalls. And Dennis has been bringing his passion for teaching to the Vetter training center since 2019. He and former electrical instructor Andreas Huber developed the two-year agile training concept. “My mission is to meet the needs of a new generation, free from a 'we've-always-done-it-this-way' approach. This also means allowing people to make their own mistakes.”
Learning by doing is still the best way to learn!
"It's less about the what," explains the 36-year-old, "and more about planning something you know nothing about. You first have to get over yourself, get going, find your place in the group, and be your own teacher, in a way. This spurs you on and gives you confidence."

As instructors, we are knowledge brokers, encouragers, and supporters.
Martin Meisterhans, Manager Mechanical Training
"First of all, it's about getting people excited and encouraging them to think for themselves. Being enthusiastic about what you do is the key to having a successful career," explains Martin Meisterhans, Mechanical Training Manager. The trained industrial mechanic started at Vetter in 2019 as a Technical Shift Coordinator. He then joined “the project” as an instructor in 2022.
The 28-year-old believes that knowledge transfer should also be fun. "And we can do that by accommodating to the different personalities, treating each other as equals, being on first-name basis, and being fair and open with one another," he adds.
Do you also want to be a Vetter apprentice?
Get all the info you need and apply. We look forward to hearing from you!