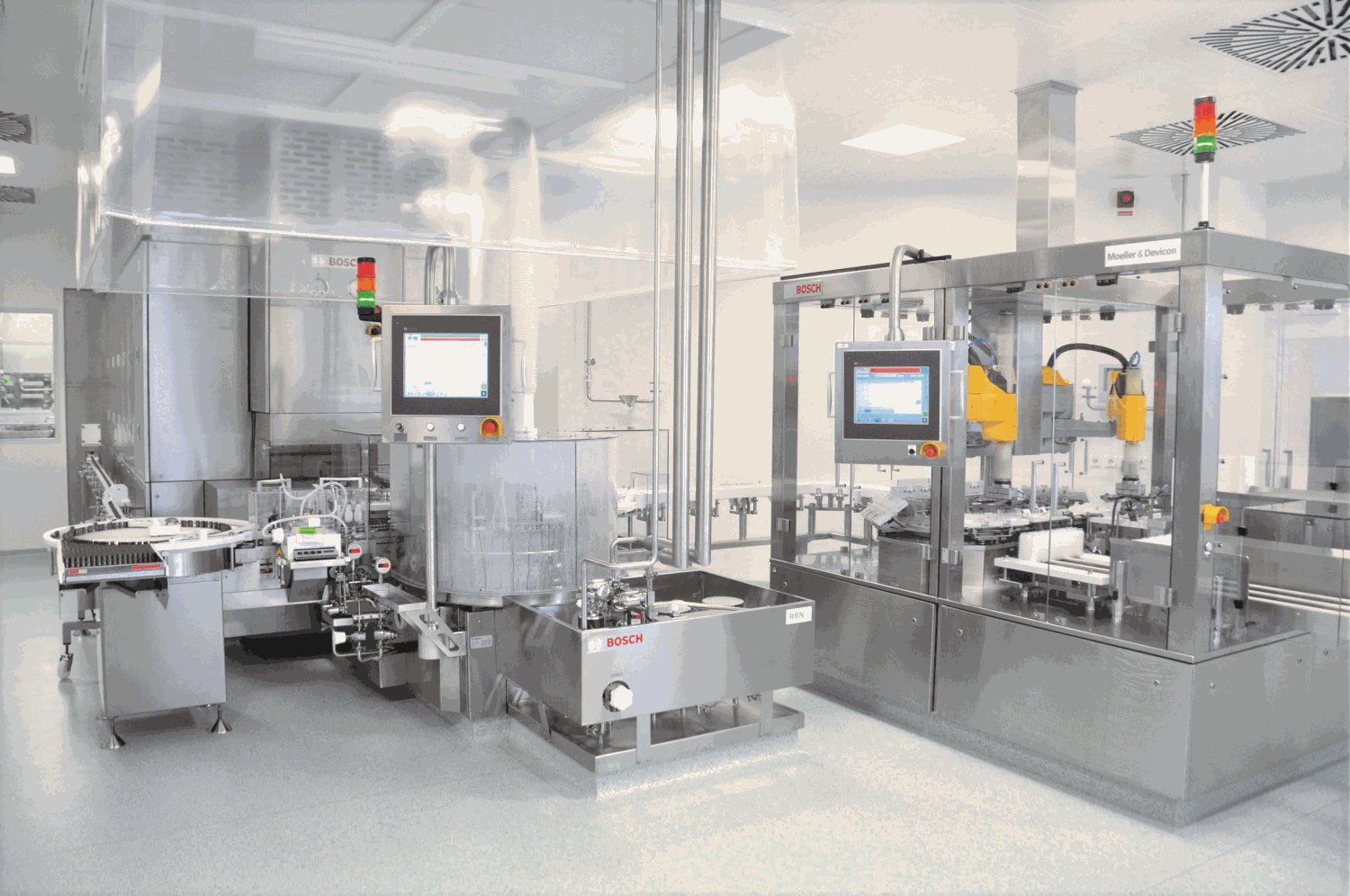
Ob große Mengen oder kleine Losgrößen mit vielen Produktwechseln: Lohnhersteller, die im Auftrag pharmazeutische Wirkstoffe abfüllen, müssen auf die sich ständig ändernden Bedürfnisse der Auftraggeber oder Anforderungen der Arzneimittelbehörden schnell und flexibel reagieren können. Das erfordert eine flexible Anlagentechnik.
Um der steigenden Nachfrage und neuen Marktanforderungen nachkommen zu können, hat der Pharmadienstleister Vetter aus Ravensburg neue Abfülllinien für Karpulen und Vials in Betrieb genommen sowie bestehende Abfüll- und Verpackungsanlagen erweitert. Der Maschinenbauer Bosch Packaging Technology, seit Januar 2020 unter dem Namen Syntegon, realisierte diese Projekte und erhielt am Ende einen Auftrag für eine neuerliche Anlagenerweiterung.
Vetter ist ein weltweit tätiger Dienstleister für die Entwicklung und Herstellung von Arzneimitteln aus Ravensburg mit weiteren Produktionsstätten in Deutschland und den Vereinigten Staaten. Das Unternehmen beschäftigt weltweit rund 4.600 Mitarbeiter und hat sich vor allem auf die aseptische Abfüllung und Verpackung von flüssigen und gefriergetrockneten Wirkstoffen in Spritzen, Vials und Karpulen spezialisiert. Die Kunden sind sowohl kleine und mittlere Unternehmen sowie Branchengrößen aus Pharma- und Biotechindustrie.
Die Bandbreite der Wirkstoffe, die Vetter abfüllt, ist groß: Dazu zählen beispielsweise Medikamente zur Behandlung von Multipler Sklerose, schwerer rheumatischer Arthritis oder Krebs; sie stellen sehr unterschiedliche Anforderungen an den sterilen Abfüllprozess. Allen gemein ist jedoch, dass Qualitätsparameter wie die Integrität der Wirkstoffmoleküle, die Sicherheit der Bediener, das exakte Einhalten der erforderlichen Füllmengen oder die Unversehrtheit des Primärpackmittels jederzeit gewährleistet sein müssen. Nur so können die Vorgaben der internationalen Arzneimittelbehörden erfüllt werden.
Bei Kunden beobachtet Vetter – neben stetig wachsenden Ansprüchen an die Qualität – einen Trend zu kleineren Losgrößen. Das bedeutet für die Anlagen häufigere Produkt- und Formatwechsel. Hintergrund dafür ist der zunehmende Bedarf an spezifischeren Arzneimitteltherapien, beispielsweise mit sogenannten „Orphan Drugs“ bei seltenen Krankheiten.
In der Summe ein Großprojekt
Um dem wachsenden Auftragsvolumen gerecht zu werden, beschloss Vetter, eine neue Produktionslinie zu beschaffen sowie bestehende Anlagen zu erweitern. So wurde die bestehende, ausgelastete Karpulenlinie in Ravensburg – auf der aktuell mehr als 25 Formate abgefüllt werden – um einen weiteren Gefriertrockner ergänzt. Damit können künftig mehr gefriergetrocknete Produkte abgefüllt werden. Ein weiteres Projekt beinhaltete eine neue Abfülllinie für Karpulen sowie eine Anlage für Vials – alles zusammen ein anspruchsvolles Großprojekt. Der passende Partner dafür war bei Vetter schon gut bekannt. „Wir arbeiten seit über 15 Jahren mit Bosch Packaging Technology zusammen“, erklärte Detlev Neuland, Technischer Projektmanager bei Vetter. In dieser Zeit haben die Maschinenexperten an verschiedenen Standorten von Vetter mehrere Abfüllanlagen errichtet und dabei „unsere Anforderungen an Technik, Prozess und Qualität hervorragend erfüllt“, fährt Detlev Neuland fort.
Glas-zu-Glas-Kontakt wird vermieden
Im Zentrum der Projekte stand eine neue Karpulenlinie für viele unterschiedliche Formate. Sie ermöglicht eine Ausbringungsrate von bis zu 12.000 Stück pro Stunde und ist freistehend im Raum konzipiert. Die Zuführung der Karpulen erfolgt vollautomatisch durch einen Detrayer, bei dem ein Roboter die Glasbehälter aus Rondo-Trays entnimmt. Danach gelangen sie über einen Hülsentransport in die Reinigungsmaschine, wo die Karpulen von außen und innen gereinigt und anschließend silikonisiert werden. Im Heißlufttunnel werden die Glasbehältnisse sterilisiert, entpyrogenisiert und die Silikonschicht fixiert. Anschließend werden die Karpulen auf einer Abfüllmaschine der MLD-Baureihe befüllt, verschlossen und magaziniert, bevor sie die nachfolgenden Prozessschritte – zum Beispiel eine optische Kontrolle oder die Endverpackung – durchlaufen.
Bis zu ihrer Magazinierung werden die Karpulen ohne jeglichen Glas-zu-Glas-Kontakt transportiert – ein Thema, das für Vetter einen hohen Stellenwert hat. Detlev Neuland erläutert: „Glas hat ein Gedächtnis. Wenn Glasbehälter sich berühren, kann es winzige Kratzer oder andere Beschädigungen geben. Solche Kollisionsfolgen resultieren in einem höheren Ausschuss, weshalb wir Glas-zu-Glas-Kontakt vermeiden, wo immer es möglich ist.“ Die Karpulen werden deshalb ab der Entnahme aus den Trays durch Hülsen geschützt, sodass sie sich nicht direkt berühren: zunächst durch Kunststoffhülsen, im Sterilisiertunnel dann durch hitzebeständige Edelstahlhülsen. Im anschließenden Abfüllprozess sorgt ein tragender Transport in der Füllmaschine für eine besonders schonende Verarbeitung der Karpulen.
Lückenlose Dokumentation inbegriffen
Auch für Kunden und Maschinenbediener bietet das Design dieser Karpulenlinie zahlreiche Vorteile, beispielsweise die Kombifüllstation mit Kolben-, Peristaltik- und Rollmembranpumpen: „Dank der kombinierten Füllstation können wir flexibel auf die Anforderungen unserer Kunden eingehen“, so Detlev Neuland. „Je nachdem, welchen Wirkstoff die Kunden abfüllen lassen, können wir das dazu passende Füllsystem anbieten.“ Eine weitere Besonderheit der Anlage ist ihr hoher Automatisierungsgrad. Angepasst an die spezifischen Belange bei Vetter lässt sich die Anlage leicht auf andere Formate umrüsten.
Ein besonderes Merkmal der Karpulenlinie ist ihre komplette Ausstattung mit autoklavierbaren Formatteilen. Dies ist ein wichtiger und spezifischer Bestandteil der Reinraumtechnik bei Vetter. Dadurch wird eine hohe pharmazeutische Sicherheit erreicht. Sie kombiniert die Vorteile von Isolatoren und Restricted Access Barrier Systems (RABS), beispielsweise durch eine automatische Dekontamination der Reinräume mit Wasserstoffperoxid vor jeder Charge.
Ein weiterer Pluspunkt der neuen Karpulenlinie ist die lückenlose Dokumentation: Von der Kalibrierung der Inlinewaage über die kontinuierliche statistische Kontrolle der Füllgewichte bis hin zum Sensorausfall werden alle prozessrelevanten Daten protokolliert und den Bedienern angezeigt. Alle erforderlichen Prozessparameter sind als Rezept im System hinterlegt. Der hohe Automatisierungsgrad vermindert zeitraubende, manuelle Einstellarbeiten. „Das vermeidet zudem Fehler im Prozess“, erklärt Detlev Neuland. „So erreichen wir eine hohe Reproduzierbarkeit und können unseren Kunden eine gleichbleibend hohe Qualität liefern.“ Dazu gehören auch zahlreiche Sensoren, die mögliche Fehler im Abfüllprozess sofort detektieren, etwa falsch gesetzte oder fehlende Stopfen. Dann werden die Produktionsverantwortlichen über Bedienterminals oder übergeordnete Leitsysteme informiert.
Neues Erweiterungsprojekt in der Planung
Zur Jahresmitte 2018 war das Großprojekt bei Vetter erfolgreich abgeschlossen. „Eine großartige Leistung von allen Beteiligten“, lautete das Fazit Detlev Neulands. „Mein persönliches Highlight war das Einbringen der fertigen Karpulenlinie in den Produktionsbereich durch einen Kran – und das, ohne die Produktion in den angrenzenden Reinräumen zu stören. Diese Herausforderung wäre ohne die exzellente Zusammenarbeit von unseren Mitarbeitern, Bosch Packaging Technology und unseren Sublieferanten nicht zu bewältigen gewesen.“ Die neue Linie ist bereits gut mit Aufträgen zur Abfüllung flüssiger Pharmazeutika ausgelastet. Das Projekt geht bald in die nächste Runde: Weil ein Auftraggeber bei Vetter zusätzliche Formate angefragt hat, planen Vetter und Syntegon eine Erweiterung der Karpulenlinie.
Veröffentlicht von neue-verpackungen.de